Back
Enviroment protection technologies
Thermal liquidation
ATERM
Non-catalytic regenerative thermal liquidation of gaseous contaminats
The main part of the plant consist in cylindrical reactor, in which the organic contaminants are liquidated in the non-catalytic thermal process. Various engeneering construction options of reactor are disigned in accordance with the required capacity. Reactor is divided into the two chambers, in them the heat recuperation and the thermal liquidation are alternated. The reactor is lined with internal insulation layer. Both above chambers are filled with ceramic packing. The air for pourification is first directed to the lower reactor’s part, throughout switching on the inlet fittings, and, after passing over both chambers, it is exhausted along with residual concentration level of organic impurities that is in compliance with emission standards. In the upper reactor’s part the temperature is automatically kept within 750-800 oC with a burner, powered with natural gas or LPG. The process heat between the pourified and contaminated air is recuperated by ceramic packing. This allows, together with quality of thermal insulation, to minimize reasonably the fuel gas consumption. Once the CxHy consentration is achived over 1.8 g/m3 in the contaminated air the whole process becomes autothermic.
Typické parametry
Volume of contaminated air |
1 000 - 12 000 m3/h |
Volume of hydrocarbon - inlet |
0,2 - 3 g/m3 |
Volume of hydrocarbon - outlet |
less than 50 mg/m3
|
Fuel gas consumption |
according to CxHy |
Unit lay-out |
5 x 8 m, heigh 4 m |
ATECHEM
Low-temperature vapor absorption into the subcooled solvent.
These are particularly suitable for racking of hydrocarbon-based fuels into in smaller volumes (petrol stations) or for chemical plants with small capacity and short term exhaust under a high concentration vapors of volatile substance. The present equipment is able to recovery of volatile substances that are exhausting into the atmosphere from various processes. Typical utilization of these units is in concentration hydrocarbons of 200 - 1000 g/m3 and in amount of the contaminated air up to 80 m3/h within the interrupted periods.
Contaminated air is cooled and washed out with subcooled liquid. Volatile substances are condensed up in the air and subsequently absorbed with cooled solvent at 95 % efficiency.
Typical parameters
Standard units capacity |
up to 80 m3/h off-gases
|
Inlet content of CxHy |
0,2 - 1 kg CxHy/m3
|
Hydrocarbons recovery efficiency |
95 % entered volume |
Installed electric output |
7 kW |
Unit lay-out |
built on surface 1,6 x 1,1 m, and 4,5 m height |
Environmental sound technology for black pitch storing
Condensation of black pitch exhaust gases - DEZA PolandCondensation of black pitch exhaust gases largely composed of indane, acenaphtehe, phenanthrene and their substitute derivatives.
Technological plant includes two change-over units. Each of them comprises two condensative stages equipped with the independent refrigerating units. There are fully automatically controlled system for operating mode of these units working in three main cycles: COOLING UP, OPERATION, REGENERATION.
The plant is installed in the outside surroundings out off the explosion hazard zone.
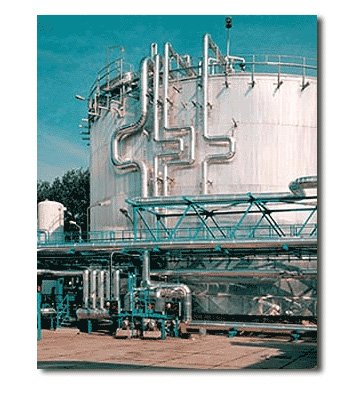
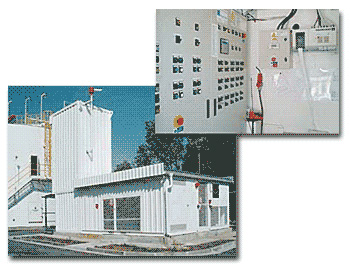
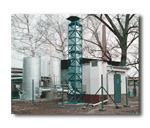